T56 Trial Fitment

The mockup motor and T56 are trial
fitted into the '71 Mustang. Modifications to the transmission
tunnel and mounts are necessary. |
With all the parts now present and accounted
for it was time to test fit the engine and T56 in the car.
With the factory motor mounts in place a hoist was used to
lower the assembly into the chassis. Using an engine leveler
and rolling the car forward a bit at a time, the T56 could
be angled down into the tunnel. The short throw shifter would
have to come off to make the turn under the car. By supporting
the tailhousing with a floor jack it was easy to see how poorly
the T56 would fit in the 71's transmission tunnel. The transmission
was pointing down almost 10 degrees in the stock location.
This was when the engine setback idea really began to make
sense. The shifter tower was hitting the tunnel brace and
it was at least two inches under the factory shifter hole.
By moving the engine back a 1.75" inches the shifter
tower would come up in the factory location and the T56 case
would better clear the tunnel bracing. This would improve
drive shaft angles dramatically alleviating driveline vibration
issues.
Setbacks
Moving the engine and transmission in a car certainly sounds
like a daunting task, but taken methodically it can often
be done quite easily. Obviously you must be comfortable in
the decision to cut and modify the vehicle. The factory's
choices in engine location have as much to do with speedy
assembly and future serviceability as it does with performance
considerations. Having the chance to reconsider where the
largest and heaviest set components fit in a car can create
real opportunities for improvement. The most obvious benefits
were moving almost 900 lbs of engine and transmission back
in an already nose heavy car and getting a lower center of
gravity with the drop. Another advantage would be added under
hood clearance for a single plane intake.
Setting the engine back 1.75" and down .75" mandated
a change in the engine and transmission mount configuration,
addressing oil pan to cross brace clearance, and making exhaust
system adjustments. The engine mounts were easy, as .75"
of setback was obtained simply by swapping the mounts side
for side, as they are offset in stock form. The remaining
1" was added by cutting the flanges off the chassis pads
and welding them to .25" plate. The plate was then drilled
to get the inch setback. To drop the engine .75" the
pads were sectioned. Incidentally, .75" was the most
possible with the factory steering link in place.
Dropping the motor down resulted in interference with the
deep-sump oil pan and under engine cross brace. Unlike earlier
Mustangs, the '71's cross brace is a spot welded permanent
structure. I had removed this some years earlier to facilitate
a pan swap without having to remove the engine. For the new
engine location I fabricated a new bolt-in member to allow
for rearward pan clearance and to allow pan removal in the
car.

Note the height of the motor mount bracket. Cutting a
section out of the middle will achieve the desired 3/4"
drop. Unbolting it from the chassis and then welding on
new plate re-drilled 1" back gets the motor .75"
closer to the desired setback.
Photo courtesy:
429mustangcougarinfo.50megs.com |

Shown is the chopped and 1" setback motor mount bracket.
The stock rubber mounts are used on the opposite sides,
which gains the additional .75" set back. |

A fabricated under engine cross-brace (top) allows for
oil-pan clearance due to the engine relocation. The original
crossmember was a welded in unit. |

The new cross member is bolted in place between the motor
mount pads. |

The custom brace clears the 460-strokers deep sump and
winged oil pan. |
|
Tunneling Through
The large dimensions of the T56 case requires the transmission
tunnel to be modified. As with all early Mustangs, the transmission
tunnel is wrapped with a brace which also serves as the mounting
locations for the the transmission crossmember. Since the
T56 would not clear this bracing, and knowing a new crossmember
had to be fabbed due to the T56's mount being 6" further
back than the C6 location, I cut out a section of the stock
bracing. This enabled the T56 to clear the tunnel and remain
at a relatively level angle.

The transmission tunnel brace is cut to offer better clearance
for the T56. |

The shifter hole in the tunnel is also modified to allow
shifter clearance. |
Fabricating a new transmission crossmember also required taking
into consideration exhaust system routing and clearance. There
needed to be clearance for the header collectors, 3.5"
exhaust tubing, and the new 3.5" driveshaft. As everything
comes together in a 10.5" wide space under the car, a
simple crossmember spanning between the frame rails wouldn't
work. Besides clearance problems with the bulging T56, a mount
of this type would also put an excessive twisting load on
the sheet metal mount points that had already been compromised
by the cuts made to clear the top of the trans. The new crossmember
had to have additional structural bracing.
The solution ended up being an integrated transmission crossmember
and driveshaft safety loop. The crossmember would bolt to
the original mounting location, except using two bolts per
side rather than the stock single through bolt. 1" x
2" by .125" thick rectangular tube was welded to
form the unit and angles back to the T56 mount location. The
driveshaft loop was positioned within 6" of the u-joint
to meet NHRA rules and secured to the frame rails with four
bolts per side. A set of braces, made from aero-shaped chrome
moly obtained from a scrap metal dealer, tie the loop and
crossmember together to form a rigid assembly.

Due to the T56 mount being 6" behind the stock C6
location, a new crossmember has to be fabricated. |

The one piece crossmember and driveshaft loop assembly
weighs 18 lbs. and provides a fully supported location
for the back of the engine and transmission. |

With downward pressure of over 150 lbs. at the mount,
plus the torque under load, the custom brace adds considerable
piece of mind and will help keep the unibody in one piece
a bit longer. |
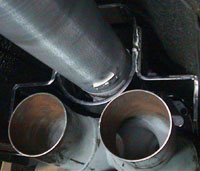
This mockup verifies proper clearances around the 3.5"
x-pipe, driveshaft and transmission crossmember assembly. |
|