
by Jon Mikelonis
Foreward
Nobody raised their pom poms when we dyno tested our Streetwise
460
build-up more than two years ago. All that could be heard
was the steady drip of tranny fluid onto machined concrete
when the motor was shutdown and the dyno results were reviewed.
The data was
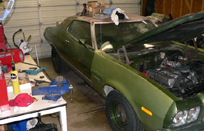
It's never been formally introduced
but Project Torino has been used in many FordMuscle articles.
Look for Project Torino in the Project
Cars section for past articles on this 1973 Ford.
|
disappointing
to say the least, with the culprit being the 10" torque
converter for the C6 tranny. The motor made a lowsy 358hp
at 5000 RPM and 387 ft lbs at 4500 RPM. On the street, the
lack of power showed in the form of very poor part throttle
performance.
First a wiped cam lobe, next an engine
fire, and now the thought of dropping the tranny to swap out
the converter, lead the Torino to the sideyard where it became
nothing more than a conversation piece. A three year conversation
piece. To add insult to injury, the site of a $450 pair of
headers resting on the front crossmember meant something was
wrong with the motor mounts used for fitting the 460 into
the intermediate chassis.
It took almost two years to recover
by pulling the Torino back into the garage for some surgery.
Somehow, overcoming your own errors and performing the same
work over again is much easier when a few years have passed.
With a clean slate and a new attitude, taking on the necessary
tasks re-emphasized that performance parts aren't always a
direct bolt-on.
Never Expect
a Perfect Fit
In the mid-90's I worked for a manufactuer within the performance
aftermarket. During my tenure, I'll never forget hearing a
perspective
regarding do-it-yourself automotive hobbysits that has stayed
with me to
this day. It went something like this...
"Enthusiasts tend to place a
large percentage of fault on themselves when
a product they've purchased does not fit their application.
This makes
them less likely to return items for refund. The phenomemon
occurs in the
performance aftermarket like no other because hobbyists are
often
embarrased to face-up to making bad purchasing decisions.
To compound the
issue, enthusiasts understand many products are intended for
stock
applications for which most are not. Because of this, they
are ususally willing to do whatever it takes to make a product
fit with their own devices."
This observation still resonates
with me because I am just like the enthusiast described above.
While some parts cannot be made to fit, if the part is designed
for the application and can be modified to work, then I'll
try it everytime. Here are three cases I experienced during
this edition of Project
Torino that prove you should "Never Expect a Direct
Fit".
Case 1: Being
Flexible with Flexplates
The first step to getting Project Torino back on track
was to swap out the
10" converter for a more street-friendly unit. Not an
easy project when working by yourself, but one that can ideally
be done in a few hours if everything goes smoothly. Smoothly?
When does anything go smoothly? Take this for example:
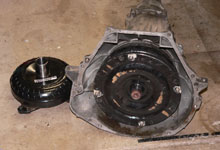
A torque converter swap usually begins with an online
order for a new
part. Not this time, I had a spare. Here's a shot of the
Big Block C6 removed from the Torino. The "old"
10" Transmission Specialties 10LS converter is shown
on the floor while the "new" 11" TCI Breakaway
converter is installed. |
|
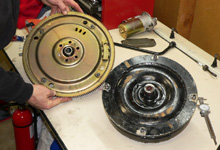
After an inital attempt to bolt up the tranny, I had to
abort the
install and drop it back down. The torque converter studs
on the
"new" TCI converter would not pass through the
installed flexplate. This is a shot of me testing both
converters on the bench with a spare flexplate. |
|
|
|

The Transmission Specialties converter uses 3/8"
studs. |
|
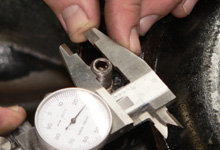
The TCI converter uses 7/16"" studs. |
|
|
|

This is the "old" Transmission Specialties converter
on the bench while test fitting the spare flexplate. Notice
the difference between the O.D. of the stud and the diameter
of the bolt hole. There's a decent amount of slack.
|
|
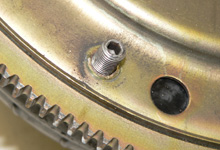
This is the "new" TCI converter with the same
flexplate test
fitted. Yes, it fits, but the stud is not much smaller
than the bolt hole. While the close tolerance is preferred,
threading the converter studs through the flexplate with
the motor in the car is difficult. |
|
|
|
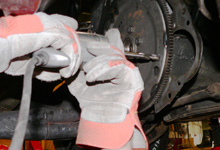
Solution? Get underneath the car and open up the holes
on the flexplate with a power drill. More |
|
|
|